POWERCORN HEATING SYSTEM FOR ENERGY GRAIN
30/50 KW
INDUSTRIAL STEP GRATE TECHNOLOGY
Our POWERCORN systems are as convenient as they are highly efficient and offer optimum economy with heating output from 30 to 75 kW. Industrial stepped grate technology enables these systems to combust free flowing fuels without generating slag.

Benefits
ECOLOGICALLY SOUND ECONOMY
Our Powercorn heating systems, with industrial step grate technology, combine maximum economy with minimum emissions. These systems can operate with wood pellets and also with energy grain (e.g. triticale and barley), as well as free flowing miscanthus or agri pellets.
Highly efficient combustion
Fuel is gasified on the industrial step grate, where primary air is supplied, at a regulated ember bed temperature of around 800 °C. The amount of combustion air and fuel charge is regulated by means of a lambda probe, so that the system achieves a level of efficiency of up to 94 %. With the aid of secondary air, the generated combustion gases are cleanly and efficiently converted into energy in a large rotating combustion zone.
Cleaning has never been easier
Where conventional heating systems still require regular cleaning, the
Powercorn system cleans the heat exchanger as well as the step grate
(with the exception of general cleaning) automatically. Large ash boxes reduce
the remaining effort to a minimum.
perfect storage
Guntamatic storage systems operate with suction discharge and screw conveyor dosing,
giving them leading operational reliability and durability. When the fuel is completely used up,
there is no need for the annual storage room cleaning.
Depending on preference, a high grade steel/mesh hopper or
sloping floor storage room with discharge screw conveyor are available.
pioneering, straightforward operating concept:
Fully automatic control of appliance and storage room functions, as well as regulation of the ambient
climate, utilising the most advanced control technology. Individual adjustments
can be made easily via the ergonomic touchscreen controller, a room control station
(if installed) or an app on a smartphone.
DURABLE QUALITY
In order to ensure that our appliances meet our high quality aspirations and those of our demanding customers, we manufacture them completely and exclusively using the best possible materials in our ultra-modern Austrian factory.
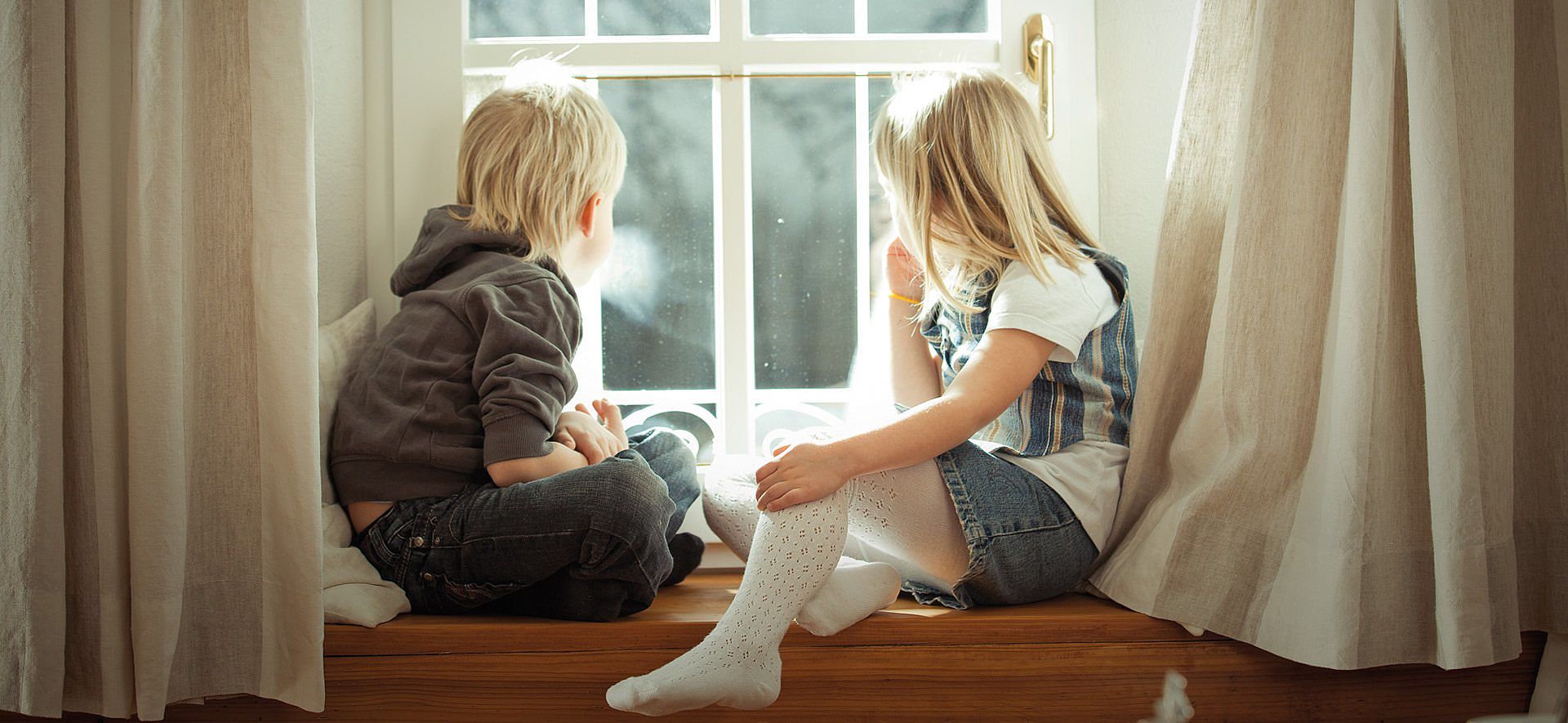
Highest level
of convenience
It's all a matter of technology
Industrial step grate technology
POWERCORN systems operate with a self-cleaning step grate which is generally only found in larger plants. This enables the ember bed height and boiler output to be adjusted in line with demand and fuel, without risking slag forming inside the boiler. The moving step grate keeps the primary air slots clean, ensures optimum combustion and also that ash is correctly discharged.
BOX
BOX containers of various sizes are available to suit the dimensions of each available storage room. The steel floor and fabric design is extremely capacious and also allows the container to be emptied completely, thereby reducing the cleaning effort. An screw conveyor-dosing vacuum discharge guarantees highly reliable operation.
FLEX
Guntamatic Flex discharge units are suitable for particularly large, intensively used, storage facilities.
The discharge screw conveyor of the vacuum discharge system has been designed for efficiency and a long service life. It offers a highly reliable operation as well as low cleaning effort,
and discharge from stores with sloping floors. Where the sloping floors are made on site, this is also a particularly affordable solution.
AUTOMATICALLY HEATING WITH ECONOMY
- Self-cleaning industrial step grate for adjusting the ember bed size and boiler output without generating slag
- Clean primary air slots and optimum combustion through moving step grate technology
- Up to 94 % efficiency
- Self-cleaning tube bundle heat exchanger ensures long operating times without maintenance or cleaning measures
- Automatic adjustment of the fuel charge, grate speed and air intake
- Suitable for free flowing agri fuels, such as triticale and barley, as well as for wood pellets.
- Ash screw conveyor and moveable ash box or fully automatic vacuum ash discharge into a 200 litre drum (option) for the highest cleaning convenience
- Well thought-out and user friendly interface with touchscreen
- Control by mobile (option)
- High grade components for maximum operational reliability
- Excellent quality and components tested several times
- First class spare parts service from our own production
- Modular pellet discharge concept, suitable for almost every situation
- Minimum power consumption thanks to energy efficient discharge
- Extremely robust pellet discharge screw conveyor with sprung arm agitator
Specification
Tabelle zum scrollen
TYPE | POWERCORN 30 | POWERCORN 50 |
|
---|---|---|---|
Fuel | Energy grain ÖNORM M7139* (miscanthus and agri pellets**), |
| |
Boiler output, energy grain | max. 25 | max. 40 | kW |
Energy efficiency class | A+ | A+ | |
Required chimney draught | 0.15 | 0.15 | mbar |
Return temperature | > 40 | > 40 | °C |
Water content | 128 | 147 | Litre |
Ash box – "grate" | 60 | 80 | Litre |
System width | 1474 | 1774 | mm |
Total weight (without stoker unit) | 562 | 667 | kg |
Safety heat exchanger | yes | yes | |
Power supply | 230 V / 13 A | 230 V / 13 A |
|
* The use of energy grain is only permissible if the regulations of the respective country allow it and the specified limits values can be adhered to.<br/> ** Generally these systems are suitable for the use of plant-based fuels. However, there are no specific type-testing certificates available for this. Use of these fuels should be checked against the relevant country-specific regulations and emissions standards.
Test report
Summary of test assessments:
"the industrial step grate technology and stainless steel lining also enables highly efficient heating with plant-based fuels (such as miscanthus); particularly low maintenance and long service life as only high grade components are used; ..."
- Tested for cleanest combustion and particularly high efficiency to EN 303-5 during 2005 and 2008 by the BLT Wieselburg and in 2006 by the TÜV BAYERN SZA
- Tested for mechanical robustness (under pressure) by the TÜV SÜD SZA
- Tested for fire safety by the IBS Linz
- Tested in accordance with the strict requirements of the European Machine and Plant Safety (CE)
- Tested for electrical safety by Ziviltechnik Stöp
- Assessment of risk analysis and CE certification by HET engineers
Awarded the Austrian Innovation Prize 2005
Awarded the Austrian Environmental seal ZU 37